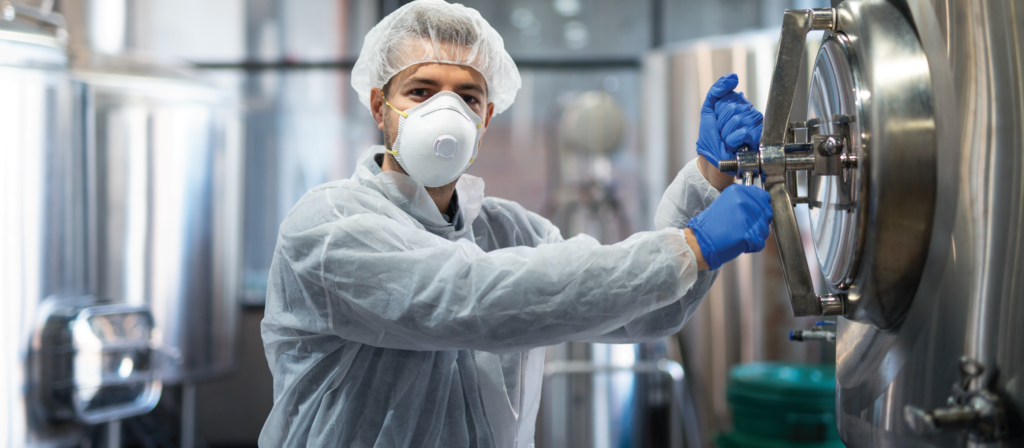
A successful organization is like a well-oiled machine, with every department acting as a part which has its own unique function and output.
And, when all these parts come together to form a comprehensive unit, their collective yield is much greater than what you would get from their individual outputs combined.
However, the key here is to have that one component which acts as a glue that holds all the different departments of the organization together; a tool that creates a synergy within the organization.
When you talk about manufacturing organizations, an enterprise resource planning (ERP) software becomes that glue.
This holds true for chemical manufacturing businesses as well.
A chemical manufacturing software has been doing the job for such businesses for many years now, integrating all the different departments of an enterprise into one comprehensive information system that’s accessible to all across the entire organization.
Many challenges, one solution – ERP
The chemical manufacturing businesses have had their fair share of challenges.
Whether into basic consumer products, or specialty chemicals, chemical manufacturing businesses operate in a highly-regulated environment.
Naturally, a lot of their time is spent in dealing with hazardous raw materials, and ever-changing and never-ending regulations such as REACH, GHS, SARA reporting, etc.
Chemical manufacturing being a complex process, managing the intricacies involved is also a challenging task for the chemical manufacturers.
Besides, the manufacturers also need to take concrete measures to protect and preserve the environment. Waste disposal management, industrial hygiene, fire hazards, and industry safety standards are some of the efforts in that direction.
Continuously improving the product quality to keep pace with the competition is another challenge for the chemical manufacturers; so is to keep innovating by ensuring adequate R&D efforts.
Changing consumer preferences, increasing item proliferation, shortening product cycle, etc., are some other challenges that test the resilience of the chemical manufacturers.
At the moment, a good ERP software for chemical industry helps the manufacturers take on all these challenges, and do a lot more.
Through its specialized, industry-specific modules as well as robust features, it allows them to maintain an optimal balance between inventory investments, customer service, and operating costs, and manage all the business processes in a safe & secured environment.
But what about the future?
The world around us is constantly changing. The technologies are evolving, and their application is driving change in different industries.
Talking about the chemical manufacturing industry, different technologies such as Internet of Things (IoT), Artificial intelligence (AI), Blockchain, Big Data Analytics, and Radio-Frequency Identification (RFID), among others, are fast gaining position of prominence.
Then there is always the risk of external factors affecting the businesses. A classic recent example can be the COVID-19 pandemic, which has had a long-lasting impact on businesses.
Majority organizations, including the chemical manufacturers, are still struggling to recover from its after-effects.
The question arises, how do the chemical manufacturing organizations fool proof their business activities?
How do they add resilience to their business operations, so that it can brave future challenges and crises?
How can they leverage the technologies of the future to their business’ advantage?
An ERP system for chemical manufacturing could be that answer, but can it do the job for them in its current avatar?
Enter Next-gen ERP
In such a scenario, manufacturers must look to discover a futuristic, next-gen ERP software that can prepare them well to address current and future issues, and keep them in a better position to remain competitive and achieve success.
Not only does the next-gen chemical ERP solution help the chemical manufacturers meet the regulatory requirements, optimize the operating costs without compromising on safety and quality standards, and indulge in continuous innovation through R&D, etc., but it also enhances the operational efficiency by adopting the latest technologies.
It also allows to rapidly develop new products in such manner that it minimizes their impact on people, environment, and the entire lifecycle.
It also embeds safety and compliance requirements along those lifecycles and monitors the impact of changes in regulatory requirements on products in real time so that the manufacturers can respond accordingly.
In such a scenario, manufacturers must look to discover a futuristic, next-gen ERP software that can prepare them well to address current and future issues, and keep them in a better position to remain competitive and achieve success.
Not only does the next-gen chemical ERP solution help the chemical manufacturers meet the regulatory requirements, optimize the operating costs without compromising on safety and quality standards, and indulge in continuous innovation through R&D, etc., but it also enhances the operational efficiency by adopting the latest technologies.
It also allows to rapidly develop new products in such manner that it minimizes their impact on people, environment, and the entire lifecycle.
It also embeds safety and compliance requirements along those lifecycles and monitors the impact of changes in regulatory requirements on products in real time so that the manufacturers can respond accordingly.
Let’s understand in detail how a next-generation ERP software for chemical manufacturing is the key to chemical manufacturing businesses’ success:
Integrated operations management:
The next-generation ERP software offers the chemical manufacturers a way to lower their stock requirement and corresponding capital costs, while improving the inventory turns.
Through the demand sensing functionality in its supply chain, it seamlessly integrates the manufacturers’ inventory management needs, production requirements, and customer demands, enabling them to make better offerings.
Support to digital technologies:
By offering integration with digital technologies such as IoT, AI, Blockchain, RFID, Big Data Analytics, etc.
The next-gen chemical manufacturing ERP allows the chemical manufacturers to improve the cost-effectiveness, become more agile, put in place smarter processes, get valuable insights in a timely manner, speedily accelerate innovation to gain competitive advantage, and create growth opportunities.
Focus on financials:
By intelligently automating the business processes, shortening payment cycles, and managing the cash flow, a next-gen ERP offers the chemical manufacturers laser focus into their finances, which in turn paves way for better future capital allocation on R&D, innovation, and automation.
Help on compliance and sustainability front:
COVID-19 has created further pressure for the chemical manufacturing industry on the compliance front.
Already being a highly-regulated industry, chemical manufacturing now needs to conform to safer working conditions, and other, even more stringent, regulations.
A next-gen specialty chemical ERP software, with its seamless ‘track & trace’ capability, audit trails, and conformance with industry/governmental/environmental regulatory obligations, helps businesses on compliance front.
Business insights for better decision making:
Laborious and manual data collection processes are highly error prone, and often slow down the decision-making process.
A next-generation chemical ERP software integrates analytics into the user experience so that every user — right from the plant manager to the CFO — has access to relevant, accurate, and up-to-date information to enable them make the right decision, every single time.
To sum up
An ERP software remains every chemical manufacturing organization’s ‘go-to’ tool, when it comes to addressing the business challenges, standardizing & automating business processes, and improving the supply chain efficiency. However, moving into the future, the chemical manufacturers must consider whether their legacy ERP systems are sufficiently agile to thrive with the changing nature of their business.
Taking a pragmatic look at their solution will give the manufacturers an idea whether their solution is holding them back or not. And, if yes, then how quickly should they move to a next-gen ERP system.
If yours is a specialty chemicals manufacturing business in need of getting a next-gen specialty chemical ERP software boost, contact us. We, at BatchMaster, understand your business’ evolving needs, and offer solutions accordingly.