ERP Module for Cost Analysis
Calculate profitable yet competitive cost
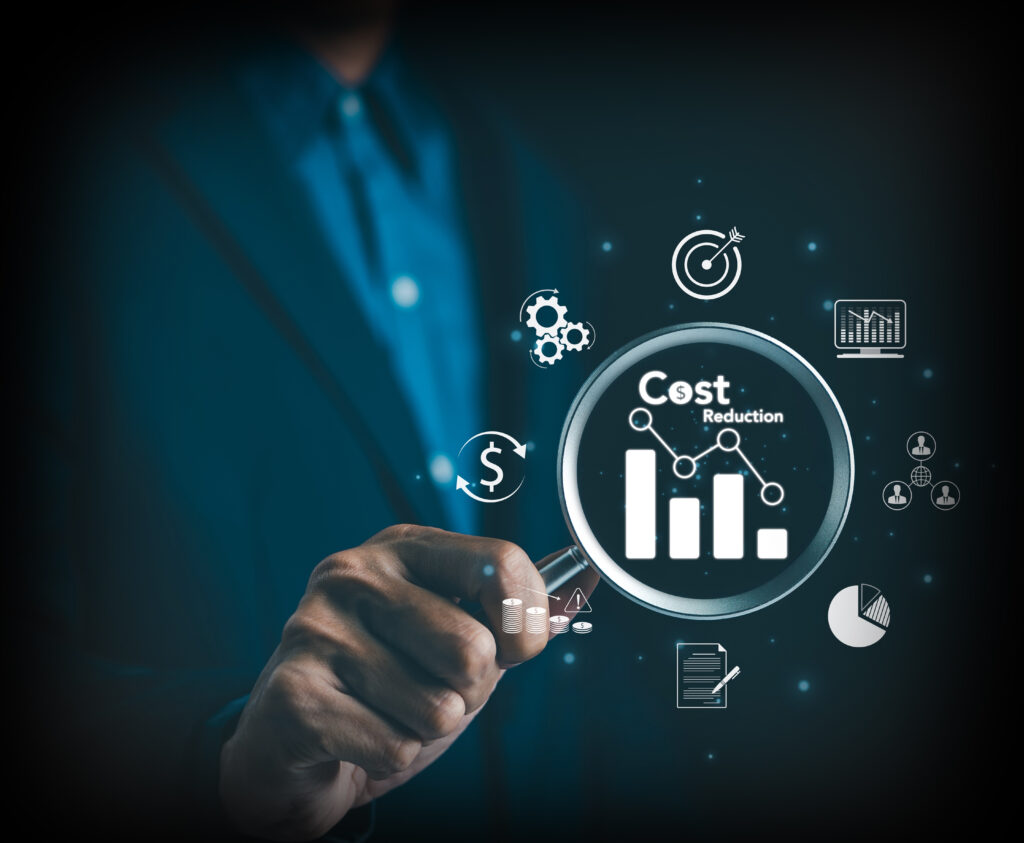
Calculate Profitable Yet Competitive Cost
Cost of your products is one of the major challenges of the managerial. Deriving a cost that's both, beneficial for the company and acceptable by customer is a challenge. But, with BatchMaster's Product Cost Analysis feature, you can rely upon advanced tools, coupled with a disciplined methodology, to closely monitor and control your costs, without sacrificing quality. With precise and accurate monitoring of all product cost factors-, BatchMaster ERP quickly calculates materials, labor, overhead, loss, and more. Offering disciplined methodology and instant detailed analysis of cost structure on-screen, it helps manufacturers reformulate to meet desired target costs.
Takes into account the costs of raw materials and consumables as well as projected costs associated to fixed setup charges, scalable labour, tiered labor, markups, margins and losses to estimate product costs during product development.<
Features that sets BatchMaster ERP’s Costing Module apart:
- Calculate cost of products based upon inventory evaluation methods
- Perform What If cost analysis
- Capture actual cost of production
- Analyze expected vs actual costs
- Being a Cost Analysis Software, it makes decisions on prices of end items to assure profitability
- Acting as a manufacturing cost analysis software, it offers product cost analysis to evaluate each formula in different sizes or containers
- Batch-sizing based upon cost, size or density or costs per unit weight or unit volume
- Roll-up intermediates to update sub-formula costs and overall costs using Last, Standard or Average costs
- Update labor and overhead
- Update finished goods to reflect changes in inventory materials costs using Last, Standard, Average or Base Cost or Market Price
- Adjust for formula loss to increase accuracy in costing, matching against historical yields
- Rely upon reports for detailed product cost, formula cost summary and product cost analysis to compare costs for finished goods in different sized containers
- Speedy cost-rollups
With BatchMaster ERP’s Costing Module you can:
- Make real-time adjustments that impact costs during product development and production
- Determine the optimal batch size based upon costs per unit weight or unit volume
- Determine which packaging configurations offer the highest margins
- Reduce overall costs to achieve higher margins
- Side-by-side comparison of products
- Identify and reduce wastage and losses
Run Our Manufacturing ERP With Your Existing Financials
Upgrade to our ERP without missing a beat in your financial and accounting routines. BatchMaster ERP offers seamless integration with Tally, QuickBooks, Sage 50/100/200/300, SAP Business One and other popular systems, ensuring a smooth transition.
Web/Cloud Deployment Available
Give your small, mid-size, or large-scale businesses the power of our ‘Cloud ERP’ solutions, and enjoy the benefits of leveraging the cloud.
Looking To Find Best Solution for Your Business?
Allow our expert team of solution consultants to review your business operations so that they can offer you the best-possible solution, either on premise or in the cloud, to meet all your industry-specific needs