Formula Management Software
Rapidly develop new formulations keeping the rapidly-changing business & consumer needs in mind
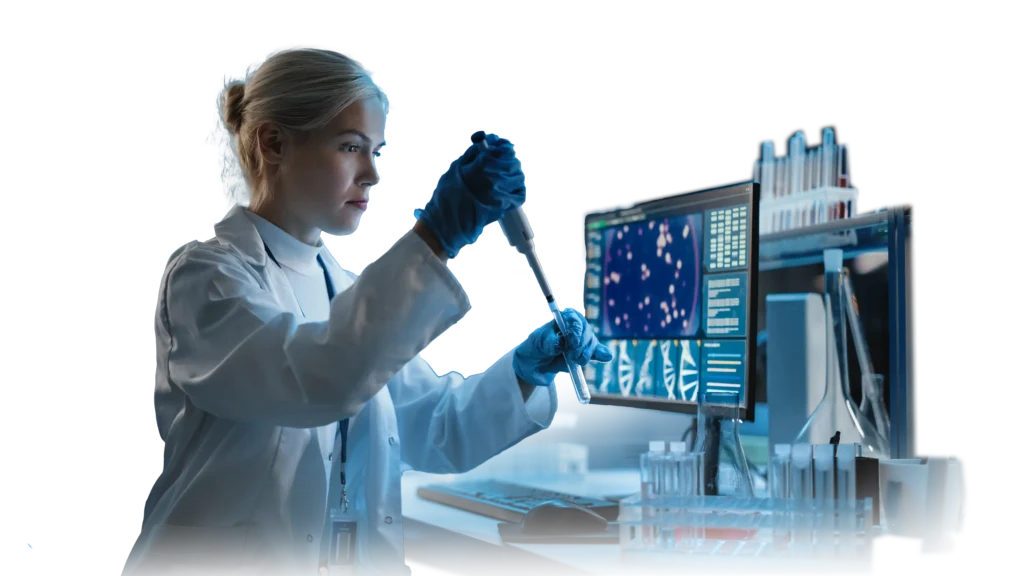
Rapidly Develop New Formulations Keeping The Rapidly-changing Business & Consumer Needs in Mind
With many business-critical operations revolving around them, the formulas, or recipes, are often considered as the life-force of a process manufacturing business.
BatchMaster offers a comprehensive Formula/recipe management module that helps innovate, store, manage, control and secure formulas and recipes, no matter their number. Besides, defining the product ingredients like intermediates, co-products and by-products,, formulation management module of BatchMaster ERP allows the product developers to embed QC tests, special manufacturing instructions and costs within the specifications. It can seamlessly integrate with standard databases helping derive formulas values/properties that are as per the standards.
This Formula Management system offers robust capabilities such as effective version controlling, automatic formula sizing, multiple units of weight and volume for ingredients, instant roll back capabilities, anytime-anywhere material substitution, etc.
Features That Engineer A Paradigm Shift In The Way Process Manufacturers Work
- Reduce your time spent on tedious, error-prone manual calculations in developing, analyzing and approving formulas
- Leverage true inventory costs within formulas
- Define fixed and variable labor costs, including consumable costs
- Estimate production losses
- Embed QC test and special manufacturing instructions in formula
- Dynamically adjust ingredients to meet target characteristics
- Analyze and compare formulas
- Manage multiple formula versions
- Employ workflow approval processes
- Unlimited inventory materials, intermediates, units of measure
- Unlimited manufacturing instructions
- Formula revision history
- "Where-used" capability by material, formula
- Size by weight, volume or physical property
- Material substitutions, if necessary
- "What-if" analysis by formula/product, container cost or physical property
- Reformulation by target value of physical property or yield
- Yield analysis capabilities
- By/Co- products calculations
- Loss factors by ingredient
- Weight, volume, density calculations
- Costing of materials, labor and overhead
- Costing by last, standard or average
Run Our Manufacturing ERP With Your Existing Financials
Upgrade to our ERP without missing a beat in your financial and accounting routines. BatchMaster ERP offers seamless integration with Tally, QuickBooks, Sage 50/100/200/300, SAP Business One and other popular systems, ensuring a smooth transition.
Web/Cloud Deployment Available
Give your small, mid-size, or large-scale businesses the power of our ‘Cloud ERP’ solutions, and enjoy the benefits of leveraging the cloud.
Looking To Find Best Solution for Your Business?
Allow our expert team of solution consultants to review your business operations so that they can offer you the best-possible solution, either on premise or in the cloud, to meet all your industry-specific needs