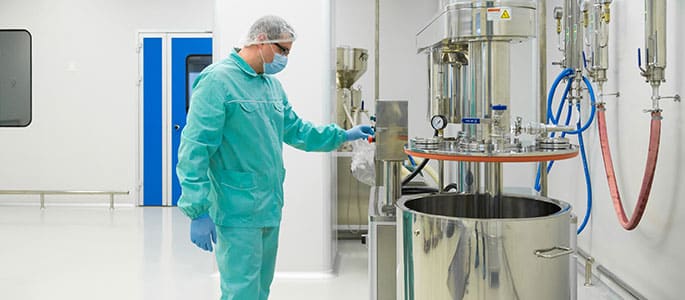
The pharmaceutical manufacturing industry continues with its upward swing, owing to the rising chronic disease prevalence across the globe, and subsequently growing demand for medications.
The growth has been further boosted by direct/in-direct factors such as constantly improving healthcare standards and rising awareness on ‘prevention being better than cure in healthcare.
Adding to these are greater penetration of health insurance that helps patients meet their healthcare expenses, increased corporate spending, and government-backed initiatives into R&D, technological advancement in treatment discovery, and the expiry of various patents over the next few years.
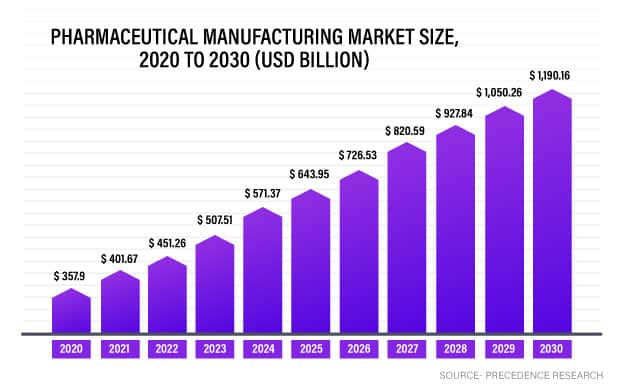
Source- Precedence Research
Understanding the Challenges-
Many challenges come along while growing a pharmaceutical manufacturing Industry. The manufacturers continue to face roadblocks on multiple fronts. There are strict regulatory requirements they have to comply with.
Then there’s the need to adapt to the sweeping healthcare reforms, negotiate with the cut-throat competition, get prepared for the unforeseeable market trends, deal with an increasingly aware consumer, traceability and quality control challenges, et al.
These challenges make things difficult for manufacturers and increase the complexity of the manufacturing process.
This is particularly harsh on the manufacturers, who as it is have a lot on their plate.
Batch Processing Makes A Way-
Operating in an industry that is highly sensitive, and which involves the manufacturing of critical life-saving medicines and equipment, the pharma manufacturers need to ensure that they are conducting their operations in a hygienic and aseptic environment.
This is where batch processing — which delivers high-quality products ‘just in time’, keeps a check on waste, and ensures that each batch is produced as efficiently as possible — comes into the picture.
What is Batch Processing?
Coming straight to the point, the method of batch processing assembles the different constituents of a product through step-by-step processes.
In this method of manufacturing, the raw materials move through the production line in batches, allowing room for a gap between steps throughout creation as a batch moves through.
In batch processing, a subsequent batch can be processed only after the current batch has finished.
In the overall process, there can be seven or more steps that are completed within the same number of equipment before a product is complete.
Talking in terms of the pharma industry, various components of a drug come together for manufacturing through a step-by-step process of batch processing.
Using this method, pharma manufacturers can produce specific amounts of a particular product and then adjust their manufacturing priorities according to the changing demands of the market.
Visual Representation of Batch and Continuous Processing-
Source- tulip.co
Some specific benefits of batch processing-
- The set-up costs are initially less expensive in the case of batch processing.
- Each batch is more easily tailored to be unique.
- Batch processing allows the use of more advanced machines/equipment to enhance the quality of the product.
- The manufacturers can easily spot the defective batches and make a new batch as a replacement. Additionally, it also helps improve production planning and scheduling.
Challenges of batch processing in pharma manufacturing
To begin with, in batch processing, it gets difficult to determine whether the plant, resources, and employees are being optimized at 100 percent efficiency or not. Also, in batch processing, avoiding costly downtime is a massive challenge.
Batch processing can be a bit tricky for the batch process managers too, as they face this mammoth task of maintaining overall control over the process.
There’s a need for them to be completely flexible while allocating resources, delegating the responsibility downwards to shop floor staff, and maintaining overall control via real-time data and communication tools, etc.
Then there’s the pressure for them to meet a ‘just in time’ production schedule, which places great pressure on every department to deliver as per the required deadline.
Testing to determine whether the final finished products meet quality and compliance standards is yet another challenge.
There’s simply no substitute for this step because a lack of testing can ruin the whole batch of goods.
Therefore, testing or quality checks throughout the manufacturing process are of paramount importance, and ensuring them, is a stiff challenge for the pharma manufacturers.
How an ERP improves batch processing?
A pharma ERP offers many potential benefits to pharmaceutical manufacturing companies. It helps them deal with the challenges that make the manufacturing process complex along the way.
To begin with, the flexibility of pharma manufacturing ERP software allows the pharma manufacturers to better their productivity even with each separate batch having distinct parameters.
Using such a system, the manufacturers can produce every single batch at the best possible efficiency.
Also at the same time can ensure the most appropriate types of equipment are selected to the best of their capacity based on specific parameters.
Reduce Batch Wastage with BatchMaster ERP-
Best-in-class pharmaceutical software like BatchMaster’s pharma ERP supports all types of batches – mix, fill, and assembly.
This means that no matter what the process type is – be it mixing, filling, or assembling – it extends support to the creation of batches for all types in no time.
Moreover, it also facilitates all the production activities from batch creation, Batch Ticket printing, allocation, inspecting, and quality checking, to final closing.
Batch Sizing is dynamically done based on weight, volume, availability of materials, or such. It lets you prioritize and expedite batch jobs while reporting shortages of ingredients and materials in the course.
BatchMaster pharma ERP’s Runs functionality allows batch production during a continuous period of operation to be achieved in individual as well as independent workable batches.
This essentially means that the manufacturers can know how many batches they need to run to achieve their target production.
Top 8 Benefits of Pharma ERP-
- It allows batches for intermediate steps to run parallel.
- Its SuperBatch functionality allows them to execute intermediates and finished goods together in a single batch.
- It offers partial closing of batches for immediate shipment of urgent orders.
- Moreover, closing a batch can be checked by mandating the execution of QC tests, inspections, and SOPs.
- BatchMaster’s Batch Processing allows following cGMP norms
- Generation of MBR and BMR is another important feature incorporated for the ease of Pharma Manufacturers.
- Batch Costs are accurately calculated considering WIP, Labor, Losses, Overhead, material costs, setup costs, and more.
- It also allows the pharma manufacturers to calculate the yield of a product during batch execution—to evaluate, maintain, and maximize the efficiency
Some other prominent features of BatchMaster’s pharma ERP include batch inspection, support to rework of excess product into WIP, alternate finished goods, or even by-product for resale, multi-level batches,
ERP Brings in Automation
What a sound pharma ERP software like BatchMaster also essentially does is that it automates the processes, and frees up the staff at the shop floor for other important things.
For ex: a pharma ERP’s automatic system checking can check the batch activity and materials, and the software can even allow the product batches that require sign-off or corrective actions, to act accordingly.
Besides, the software also records all activities and audits to a database for any future reference.
The need for security and traceability for consumer products such as pharmaceuticals has never been this high before.
And rightly so, a pharma ERP helps the manufacturers track the manufacture of batches from raw material to the finished article—fostering both traceability and transparency.
Also, it gives the manufacturers the ability to trace every product as quickly as possible if problems occur, and even for the audits.
BatchMaster’s BMR (Batch Manufacturing Record) and MBR (Master Batch Record) functionalities come in handy in this regard.
BMR are documents that help manufacturers ensure quality and regulatory requirements are achieved, while MBR are general manufacturing instructions – a prerequisite for cGMP – which lay the foundation for a precise, detailed description of a pharmaceutical manufacturing operation.
Furthermore, using pharma ERP software, regulatory requirements can be addressed, and Formula bills of material (BOMs), packaged and batch entry BOMs, batch sheet and ticket processing, private label, custom orders, bills of lading, and other manufacturing processes can be simplified.
In fact, pharmaceutical software gives the manufacturers the ability to look beyond the regulatory requirements, and carry out incisive testing to gain more knowledge of the risks that possible contaminants could have on any drug being manufactured.
Conclusion:
It is clear from the blog that for pharma manufacturers deal with the various challenges, and to improve batch processing, a tool as competent as the pharmaceutical software is a must.
A flexible pharma ERP software not just helps them seamlessly link all departments and processes from sourcing, and manufacturing to shipping, but also manages quality and compliance, streamlines the operations, maximizes productivity, reduces costs, increases profitability, and improves supplier relationships, among other things.
BatchMaster ERP for pharmaceuticals helps the manufacturers integrate all the processes such as planning, purchasing, sales, inventory, marketing, distribution, regulatory compliance, etc., and allows their pharma manufacturing business to operate more efficiently and profitably. Contact us today for more information.