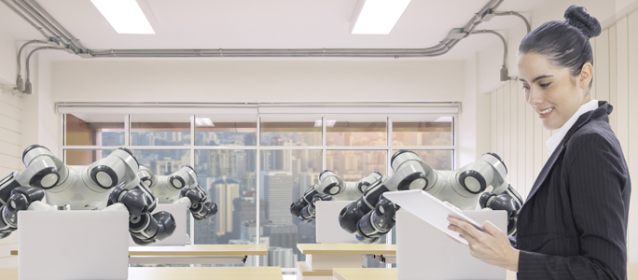
We all have grown up hearing the adage “change is the only constant.” And don’t we all agree with it? We all face change almost on an everyday basis, and in the different aspects of life.
It could be a change in routine or schedule, a simple change in weather, a change in government or local administration’s rules & policies, a change in someone’s mood or behavior, so on and so forth.
We tend to change our old vehicles, clothes, mobile phones, accessories, etc. Some people change their jobs frequently, some other change partners.
In a nutshell, change indeed is the only constant in life, the only thing we can be sure will happen.
A lot of times change also comes with responsibility. Talking in context of business world, manufacturing organizations embark on change initiatives from time to time.
It could be anything- going lean, improving quality, or customer service, streamlining the operations, cost reduction- anything. However, merely planning an initiative is not enough.
The real challenge lies in getting it implemented along with organization-wide acceptance.
This is where a ‘champion of change’ comes into play.
A champion of change is the person from the top leadership who is accountable for implementing the change initiative and ensuring that it is being accepted across the organization.
A champion of change also happens to be the person who brings about a transformation within the organization; one who ushers in the organization in a new era by breaking the shackles of the past; one who improves the business processes for good.
Many manufacturing businesses are today looking to have the champion of change in their organization, with their archaic businesses being in dire need of change, complete overhaul, or modernization.
Operating on antiquated systems, their businesses are facing a plethora of operational challenges.
This is why the manufacturers are looking for tools such as an ERP, or going for ERP integration with SAP Business One, so that they can bring about the desired change.
How traditional businesses have been functioning thus far?
Majority of the traditional manufacturing businesses either use outdated systems, or disparate systems, i.e. different software for different business needs.
Worse, some of the businesses still don’t use a software, or are into manual data entry, which wastes a lot of their productive time. Besides, the method is highly error-prone.
Such businesses don’t get accurate reports in real-time, and invariably end up wasting a major chunk of their time validating reports from multiple platforms.
Not only this, as all such businesses struggle on other fronts too.
They have absolutely no hold over their day-to-day business activities such as cash flow, inventory levels, sales orders, production orders, etc.
Talking about the cash flow in particular, the conventional approach of such businesses has been to control costs and monitor the cash flows using static spreadsheets and paper reports.
Then there are quality and traceability issues, lack of planning which leads to inaccuracies in scheduling, issues managing the costs as well shrinking profits, etc.
To get out of this mess, the manufacturers need a competent tool like SAP Business One, or ERP integration with SAP Business One for their existing ERP system.
Riding the SAP Business One transformation wave
The modern-day manufacturers are fast realizing the need to do away with the traditional ways of running manufacturing operations.
They understand and acknowledge the fact that data-based insight can have massive influence on their business’ growth, and in particular, can have a huge say in decision making for their business.
They are increasingly getting aware that in order to achieve growth, they need to identify emerging markets, evaluate growth opportunities, and look for new areas for investment.
And one tool that can help them with all of this by providing a real-time view into the business operations, valuable data-based insight, and an enhanced collaboration across different business functions with seamless flow of communication, is SAP Business One.
SAP Business One is a comprehensive, all-in-one robust business management solution which takes care of your manufacturing business’ different functions such as finance, sales, inventory control, human resources, customer relationship management (CRM), warehousing, production management, purchasing and procurement, and reporting and analytics among others, and allows you to run your business in the best-possible manner.
A supremely flexible solution, SAP Business One is easy to use, inexpensive and very quick to implement.
With real-time access to critical business data, the manufacturers are now becoming driver of corporate strategy, steering the company in a profitable direction based on data-driven insights across every department.
As a standalone software, or after integration with an ERP, SAP Business One delivers tremendous value for manufacturing businesses in general, and process manufacturing in particular, when integrated with an ERP tailored for the industry’s needs.
BatchMaster Manufacturing for SAP Business One –
a process manufacturing add-on for SAP Business One – is one solution for the process manufacturers that stands out with its exceptional capabilities to handle all the distribution, manufacturing, finance, quality & compliance needs of your process manufacturing business.
Here’s a rundown on some of the features/benefits of SAP Business One ERP / ERP integration with SAP business one, derived from SAP Business One modules, that have helped the modern manufacturer become a champion of change:
Greater flexibility:
The framework or say the architecture of SAP Business One, whether used alone or in integration with other ERP solutions like BatchMaster Manufacturing, is completely and quickly adaptable to changes that frequently take place in business in terms of processes, compliance requirements, new business requirements, etc.
Moreover, being an all-in-one system, it enables performing all operations from a single platform and letting information to stream as soon as it enters your framework.
This renders the much needed flexibility across your product development to maintenance, management and control.
Improved efficiency
SAP Business One eliminates the need to maintain data manually and waste unnecessary time, as using it the businesses can store all their relevant business data at a single place in a one-time activity.
The time manufacturers save can be used for other activities that add value to their business, such as R&D and launch of new products, exploring new business avenues, etc.
Its in-memory computing Platform SAP HANA, supercharges the speed of information fetching, thereby saving a lot of time, accelerating process and thus enhancing efficiency.
Increased scalability:
SAP Business One is adaptable in nature, and has tremendous scalability which means it changes and grows in the same way your business does, irrespective of your IT infrastructure- Cloud or on-premise.
It doesn’t come with any restriction on number of users and storage capacity.
Besides, it prepares the manufacturing businesses to take on new markets, handles substantial increase in transactional volume, workload and amount of data, comes with global capabilities, easy integrations and accommodates business expansion.
Informed decisions:
With its real-time updates, alerts, reminders, and numbers that are vital for business’ day-to-day functioning, SAP Business One creates a system from which manufacturers can have a 360-degree view of their business’ actionable information.
Using this information through SAP Business One’s Dashboards, personalized workcenters, alerts, customizable reports, etc., the manufacturers can make informed, accurate and timely business decisions.
Increased customer satisfaction & profitability:
With faster access to all the critical business data, manufacturers are better placed to respond to their customers in the shortest-possible time with SAP Business One.
Other benefits of SAP Business One including faster turnaround time, prompt service, knowledge about purchasing patterns, effective grievance redressal etc.
It helps manufacturers win over their customers and clock in more sales, which translates into more revenue and higher profit.
Also with SAP Business One, the manufacturers have all the time in the world for R&D and launch of new products.
Wrap up
By using SAP Business One, or through ERP integration with SAP Business One (like BatchMaster Manufacturing for SAP Business One), modern-day manufacturers are not just ridding their businesses of outdated systems and business practices, but also bringing in a host of positive changes for them.
With their businesses becoming more modern, agile, responsive, flexible, efficient, scalable, and profitable, the manufacturers are truly becoming the champion of change using SAP Business One.
BatchMaster Manufacturing for SAP Business One is built-in SAP Business One platform, and not integrated, rendering its process manufacturing capabilities to the latter and making it one complete solution capable of handling unique needs of process manufacturers be it related to innovation, formula/recipe management, batch-processing, product costing, quality, compliance or managing the supply chain end-to-end.
Write to us today to know more on how we can help your pharmaceutical, food & beverage, paint & coatings, specialty chemicals, or cosmetics manufacturing businesses.