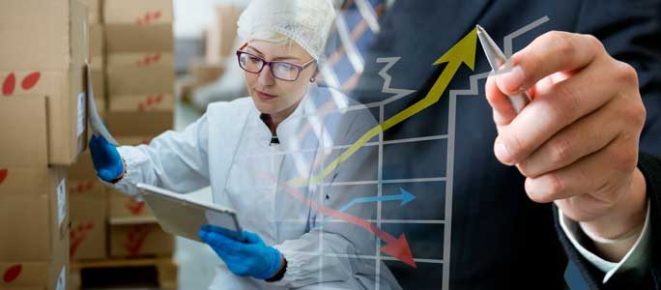
That an Enterprise Resource Planning (ERP) software is an indispensable part of process manufacturing industries – or even the manufacturing industries in general – is not headline-worthy stuff anymore.
For all its apparent benefits to the manufacturing industries, which include effective management of their business processes, streamlined operations, and real-time data with impeccable accuracy, enhanced profitability, increased efficiency, and much-improved decision making, there’s simply no substitute to an ERP for any manufacturing industry.
Bringing all the business functions on the same page, it standardizes and integrates business processes across different departments such as production, procurement, planning, costing, warehousing, and Quality Control (QC), among others.
There’s another crucial area of a manufacturing business which is well taken care of by the ERP software, and that’s supply-chain management.
It ensures end-to-end management of the flow of raw materials, the inventory in use, and the finished products.
In short, it streamlines the entire supply chain, and ensures that any possible roadblocks such as inventory shortage, inventory wastage, and wait time don’t hamper the flow of products across channels.
ERP software makes this possible by giving the manufacturers a tight control over material management, a core function of the supply-chain. That’s precisely why material requirements planning is so significant in manufacturing industries.
This blog endeavors to take a look at material requirements planning, and how it supports the process manufacturers. To begin with, let’s understand what material requirements planning is.
Material Requirements Planning
In manufacturing industries, determining the right amount of raw material to meet the current and future demand is a perennial challenge.
The manufacturers always feel the heat, for if they underestimate the quantity, they will face raw material shortage and their clients will be forced to seek the products from other sources.
At the same time, if they overestimate the quantity required, it will result in either inventory wastage, or space blockage- a monetary loss in both cases.
This holds true for process manufacturers as well, as they too invariably rely on the balance between supply and demand of the raw materials.
So, talk about a bakery industry, a pharmaceuticals manufacturer, a manufacturer who’s into paper & packaging products’ manufacturing, or someone who manufactures automotive paints, having a materials requirement planning software can significantly benefit their business operations.
To define it in simple words, MRP is a means for calculating the materials needed to manufacture a product.
Available as module in the process manufacturing ERP software packages, it assists production managers in scheduling and placing orders for the required items, and to maintain a healthy flow of materials required for production.
The MRP module allows the manufacturers to determine which raw material needs replenishment, and hence needs to be ordered, when to be ordered, in what quantity to be ordered, and when the delivery of the order should be scheduled.
How MRP supports process manufacturers?
The primary objective of any process manufacturing business, or any manufacturing business for that matter, is to ensure that the raw materials are available at the shop floor at the right time in right quantity, so that the manufacturing takes place on schedule.
It is the uninterrupted flow of raw materials that allows manufacturing businesses to function smoothly.
Especially talking about the process industries like pharmaceuticals, cosmetics, food & beverage or paints manufacturing, the manufacturers often rely on raw materials derived from nature with limited shelf life.
Sourcing the raw materials for such manufacturers proves to be extremely difficult, owing to the stringent environmental regulations and expiry troubles.
Every business needs raw materials, and thus looks to purchase, and store the right quantity of stocks of materials for immediate as well as long-term requirements.
Blame it on the rising raw material costs and increasing warehouse rents, the significance of managing and planning the availability of raw materials is increasing more than ever.
And this is where MRP chips in, proving to be an integral function of any process manufacturing business. It takes care of the processes that include activities of acquiring materials, be it raw material, packaging material, supporting material, non-inventory or others, controlling their procurement, and managing their flow and supply to different places in the right quantity at right place and time.
This way, it helps ensure that there is enough component available for production, and the finished goods are ready and shipped to the customer on time.
How exactly and dynamically it does so?
MRP system allows the manufacturers to view the production bottlenecks at a glance with interactive graphical vision.
This way, the manufacturers can act proactively, and ensure material availability.
It checks for the production schedules in the defined frame (i.e. the period for which material needs to be planned, say a day or days, weeks, months or an entire year) for an item or a group of items.
Based on the schedule, it calculates the quantity required of the item. It then carefully checks for how much quantity of that order is already available, how much is ordered and expected to be received before it is needed or if it is available at other warehouses of the company and can be procured from there.
Subtracting the quantity available or expected, it suggests ordering the balance quantity. Some MRP system also suggests the date on which and the vendor from whom the material should be procured.
The date is suggested considering the vendor lead time, the quality lead time, quarantine days if any, etc.
This is how it ensures that the right quantity is available at the right time. If there’s any change in the requirements or demand or sudden unexpected orders crop up, the MRP systems even suggest which orders you should try to expedite.
All this is done in just a few clicks without the long, complicated and complex manual calculations that are certainly error-prone.
This entire process results in optimized inventory, reduced wastage, improved inventory turns and promotes better use of the working capital, thus facilitating cost reduction.
By having only as much inventory as required, manufacturers can save significantly and even avoid the rental costs. And in turn, the capital saved can be used elsewhere, for other productive jobs related to the business.
To sum up
MRP ensures that materials and components are available when needed in the production process and that manufacturing takes place on schedule.
And a process manufacturing ERP system loaded with MRP functionality makes it possible for the process manufacturers to manage the entire process smoothly, and brings in a host of benefits such as better material control, inventory optimization, cost reduction, improved handling of materials, timely availability of materials in right quantity, and enhanced productivity, among others. One such materials requirements planning software is BatchMaster ERP, a best-in-class process manufacturing ERP that helps manufacturers run their business efficiently. For more information about it, reach out at sales@batchmaster.com