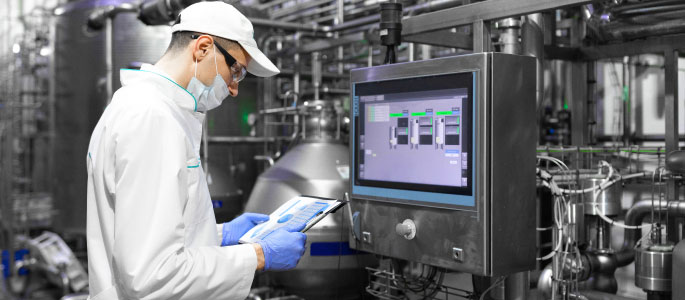
A formula/recipe is a set of instructions to combine ingredients or raw materials in a certain ratio with the help of machines and labour. For process manufacturing, a formula specification is expected to produce one or more finished products in bulk quantities.
A formula/recipe is the holy grail of process manufacturing. A business can’t be run without a product and a product doesn’t exist without a formula. Product development in a manufacturing business starts with a formula and only upon arriving at the perfect mix of ingredients can production be started. Therefore, a formula can be understood as the building block of everything that a process manufacturing business is expecting to achieve.
Moreover, process manufacturing facilities invariably produce multiple products at any given time. Hundreds and even thousands of iterations of many different formulae for multiple products are worked upon, until the perfect mixes are achieved. Therefore, the formulae/recipes for all those products need to be carefully segregated from one another and preserved for further research.
Moreover, formulae basically contain the standard specifications. However, during production, they need to be scaled to meet the targeted output. Scaling the formula for mass production is a tough task and should be handled carefully. The dynamic demand for products makes it necessary for manufacturers to be prepared for scaling up or down from the ideal production quantity with respect to the needs of the market. The vast variation in the physical, chemical and biological characteristics of materials needs to be monitored carefully and recorded accurately. Even a small mistake can lead to irreversible changes in the properties of the final outcome.
The advent of ERP…
Companies spend years working on different formulae for their products and casually save them in easily pregnable excel sheets. A document as important as a formula must be protected and therefore, should be saved in a restricted-access environment. Also, managing and navigating through so many excel sheets can prove too cumbersome and error prone. Therefore, a formula management module embedded into an ERP software helps manufacturers record, store, change, compare and scale formulae, while protecting it from any unwanted access.
Food, pharmaceutical, chemical, paints & coatings, cosmetics and other industries might be different in other ways, but they all have the same requirements when it comes to formula management. Along with defining the product ingredients and quantities, a formula ERP software allows product developers to embed QC tests, special instructions and production costs into the process.
Benefits of ERP for formula management…
Formula management helps in developing and maintaining superior products. Below are the benefits of implementing a formula management software in a process manufacturing business:
- Formula Creation, Correction and Version control – With ERP software, businesses can create and manage formulas/recipes for multiple products. After creation and testing, ERP also enables product developers to continue append the formula and create better versions without impacting the master formula being used in production. Moreover, if you are operating on a particular formula and want to go back to a previously existing entry, ERP helps with version control as well. You can also store as many formulae as you like and access them on the go.
- Fostering Innovation – Rapidly changing customer demands are fueling innovation. ERP unlocks innovation through dynamic, what-if calculations to achieve targeted nutritional, chemicals, cost and such values, all this without laborious, error-prone calculations. Multiple formulas can be compared and analyzed side-by-side to select the most-profitable one.
- Formula Scalability – Process manufacturing is a dynamic business. Product demand can rise and fall according to seasons and opportunities. Manufacturers need to be prepared to produce different quantities without changing the composition of the finished goods. In such situations, ERP lets manufacturers run simulations with varying inputs and test the outcomes. This helps manufacturers plan production quantities in perfect proportions without any hinderance in product quality.
- Support for Multiple Packaging Options – Cooking oil, jam, cough syrup and similar batch produced goods are sold in multiple packaging with different weights and volumes. Rather than being BOM based, ERP is a formula-based software, which enables manufacturers to add ingredients in prescribed proportions in terms of weight or volume. This saves the additional process of constantly adjusting the formula for each type of packaging.
- Support for Multiple UoM – Materials with different UoM or Units of Measure can be used to produce finished goods. The raw material may be weighed in KGs while the finished goods might be measured in liters. ERP supports the conversion of materials from one unit to the other and even provides mathematical calculations for the same. These calculations can also be used for scaling the formula in different proportions and preserving product composition.
- Product Costing – ERP can help with adding up the direct material, direct labor, and overhead costs to obtain the total manufacturing cost per unit. ERP can also run simulations of production runs with different quantities for organizations to achieve optimum costing for every product batch. Additionally, ERP can separate product cost from packaging bills-of-material (BOMs) to ascertain the manufacturing and packaging costs separately.
- By-products & Co-product management – Formula management system can help in storing, managing and costing by-products and co-products. While developing the recipe/formula, product developers can easily define the by-products and co-products that will be obtained during production. These products add to the total yield of the production process and can be sold separately, making the business more profitable.
- Improving Compliance & Quality – Compliance with various regulatory bodies like cGMP, HACCP, GHS, FDA and other guidelines is necessary & if it’s taken care of in the product development stage, the business can rest assured to not make any compliance mistakes. What-if analysis and data integration with USDA/Genesis can help manufacturers achieve the targeted nutritional values. Audit trails in formula ERP software keep a record or say trail of all the creation, modifications and deletions done to a formulae.
In addition to these benefits, labelling your products with correct ingredients, nutritional values & allergen information can also be achieved with the help of ERP.
Formulation management should be one of the most important motivators to implement an ERP system in your business. If you are looking for a competent ERP software with enhanced formula management capabilities, you should contact BatchMaster. If you want to know more about BatchMaster ERP, click here.