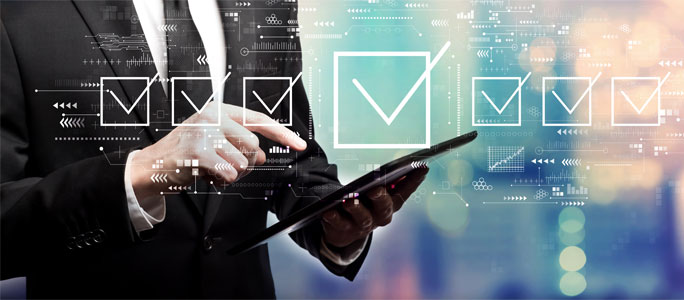
More and more businesses are now giving prime importance to the quality. But if your manufacturing business is not one of them, you perhaps need to learn its importance.
Understand it this way. If any of your business processes is operating at 99 percent efficiency, it will produce 10,000 defects per million parts. This is over 2,941 times more than what the excellent organizations allow.
The best businesses in the world allow for no more than 3.4 defects per million parts in manufactured goods, or 3.4 mistakes per million activities in a service operation, which means their processes ought to be 99.99966 percent perfect to achieve those results.
This is called the six sigma approach to Total Quality Management.
Let’s keep the discussion over six sigma for some other day, and talk about Total Quality Management, or simply TQM.
Let us also understand how it complements an Enterprise Resource Planning Software, or simply ERP software, in improving overall quality within an organization.
Key Takeaways:
- Total quality management is a continuous process of identifying and reducing errors/issues.
- The primary goal of Total Quality Management is to continuously improve an organization’s internal processes. This eventually increases the quality of its outputs.
- Total quality management emphasizes on all the parties involved in the production processes.
- It ensures top-quality products, streamlines the supply chain cycle, enhances customer service, and makes sure that the workforce is trained.
Total Quality Management typically has eight guiding principles that range from focusing on customers, continually improving, and adhering to processes.
Definition of Total Quality Management:
Total Quality Management is a manufacturing philosophy. It focuses on improving quality across the operations and producing higher quality products with few defects.
At the core of this approach are concepts such as customer satisfaction, and continuous improvement.
It is often associated with concepts like just-in-time inventory, and just-in-time manufacturing.
Basically, a TQM approach makes all members of an organization participate in continual improvement of:
- Processes
- Products
- Services
- Organizational culture
With an emphasis on delivering defect-free products/services to the customers.
The TQM approach uses different tools such as strategy, data, and effective communication to integrate the quality discipline into the culture and activities of the organization.
TQM’s objective is to do things right the very first time, every time, so as to reduce cost, and save time required to correct poor work, and failed product and service implementations.
History of Total Quality Management:
The roots of Total Quality Management can be traced to Walter A. Shewhart’s introduction of modern quality control in the early 1900s.
In 1931, Shewhart published a seminal industrial book titled “Economic Control of Quality of Manufactured Products“.
The book explains the basic and essential principles of manufacturing quality control.
Later advancements on Shewhart’s work led to the development of new quality management standards.
After that, Joseph M. Juran also published a book named- What Is Total Quality Control? – In 1954, but in a Japanese style.
The project was inspired by Juran’s visit to Japan at the invitation of Japanese engineers and scientists.
Later, Juran co-wrote Quality Planning and Analysis, another TQM greatest best-seller of that time.
W. Edwards Deming played another important role in the development of TQM.
After the Second World War, Deming was also transferred to Japan, where he was associated with the Union of Japanese Scientists and Engineers (JUSE).
Deming’s 14 Points, Deming’s Seven Deadly Diseases of Management, and The Deming Wheel are just a few of the TQM frameworks he worked on throughout his career.
8 Principles of Total Quality Management
Customer focus:
The organizations depend on their customers, who determine the level of quality.
They must hence strive to understand their customers’ current and future needs, and work towards exceeding their expectations by continually improving the quality, processes, etc.
It results in increased customer loyalty, revenue, and reduced waste.
Leadership:
Business without strong and clear leadership is often directionless and failure prone.
TQM’s second principle suggests an organization must have strong leadership and clearly defined objectives; and its employees must actively work towards achieving those targets.
Employee involvement:
The third principle is in a way an extension of the second principle, as it states that Involvement of all the employees of an organization is essential in the development of quality products or services.
This ensures increased motivation and accountability amongst the employees, and paves way for innovation in products as well as services.
Process-centred approach:
Organizations must develop processes in accordance with their vision, mission, and strategies.
These processes help them to drive efficiency and effectiveness, and eventually productivity.
Such processes, when executed consistently, help the organisations in following ways:
- Speeds-up the overall organizational work
- Reduces cost
- Promotes continuous improvement
- Helps deliver quality to the customers.
Planned and organised approach:
Organizations must focus on two things:
- Managing the key processes
- Setting processes together as a system to get greater efficiency
A planned approach or carefully thought management is thus essential to ensure that quality becomes the core aspect of all business processes.
Continuous improvement:
Any organisation can follow the mantra of continuous improvement. This improvement can be in the process it follows, or in techniques it uses.
The purpose of such improvement is to produce better quality products, be more competitive and raise expectations of customers.
Thus, to be unique and create a special market for itself, organisation must follow regular improvement approach.
Realistic approach to decision-making:
If you own an organisation, and take important decisions on gut-feelings then what will be the future of your organisation? Yes, anyone can easily answer that the organisation will struggle to survive.
This is because intuitions can be wrong, but data and its interpretation cannot.
Therefore, organisations need real time data and its analysis to take important and business- crucial decisions.
Here comes the role of Total Quality Management. It brings realistic data in the organisation.
With this data, organisation can improve productivity, quality of product and take a better market share.
Mutually helpful supplier relations:
This is based on a simple idea. The idea is supplier and organisations are interdependent. Strong relations between them can increase productivity and create value.
The result is improved cost and better utilization of resources for both sides, and smooth work practices. This eventually enhance customer satisfaction.
Advantages of Total Quality Management:
A company can reap the following benefits if it implements TQM:
- Produces a product in less money.
- Produces consistent products.
- Reduces waste and increase quality.
- Increases customer loyalty.
- Can adjust with change easily.
- Saves on material, distribution, sourcing, back-office function
- Enhances competitive position
- Improves market image
- Higher profitability
- Improves customer focus and satisfaction
- Increases customer loyalty and retention
- Improves employee morale
Industries that use Total Quality Management:
As Quality is always co-related with the manufacturing sector, its principles can’t be left untouched by its numerous industries.
Total Quality Management provides a cohesive vision for systematic change to industries that want to focus on long-term change rather than short-term goals.
And so, TQM is used in many industries, including, but not limited to, manufacturing, banking and finance, and pharma.
What is the goal of Total Quality Management?
Company can run to earn profit when all the activities and process are set in a fashion to meet standard output. TQM ensures that company follows the rule.
These activities and process include developing and documenting quality policy, carrying out quality standards, and quality controls initiatives.
Examples of Total Quality Management in real-life:
One example of TQM is the automaker Toyota. Toyota improved the quality of its products and labor across the board by implementing TQM and kaizen.
In 1949, Toyota implemented a related technique known as statistical quality control (SQC).
Tata Steel, an Indian component of the Tata Group and a steel-producing corporation, is another example of TQM in action.
In the 1980s, Tata Steel implemented TQM. In 2008, the business received the Deming Application Prize. To have a thorough grasp of its consumers, Tata Steel adopted TQM approaches.
Relation between Total Quality Management & Enterprise Resource Planning
TQM and ERP software complement each other. TQM is a predecessor of ERP implementation. They both share common goals.
The effective use of TQM provides a much higher quality ERP implementation.
The objectives of both the systems are improving customer satisfaction, productivity and efficiency, increasing competitiveness, and reducing waste, among others.
TQM ensures satisfaction of all the stakeholders, including ERP vendors, service providers, system integrator, team members who implement the software, and the company that purchased the software.
Qualities of TQM are basically common to all different types of business process flows and ERP functional modules.
ERP software, on the other hand, play the role of an enabler of the TQM principles and philosophies.
In context of a manufacturing business, ERP software help achieve the aforementioned goals and obtain the maximum return on investment from expensive investments, when used in collaboration with TQM.
The benefits of this union are unparalleled, for the organization develops problem solving techniques and continuous improvement opportunities.
With both of them working jointly, businesses can eliminate waste, drive production and satisfy customers more than ever before.
And their benefits can be leveraged in every area of the business, not just the shop floor.
Concluding statement:
Quality management is a planned approach towards the quality improvement of an organization. It tells all the employees about the process to follow for developing a culture of quality.
When operational quality is improved, the quality of product increase. This increases customer satisfaction and thus customer loyalty and repeat business.
If you want to adopt Total Quality Management in your organisation and streamline quality process, send an email to contact@bmqualitymaster.com or for detail, visit our website.