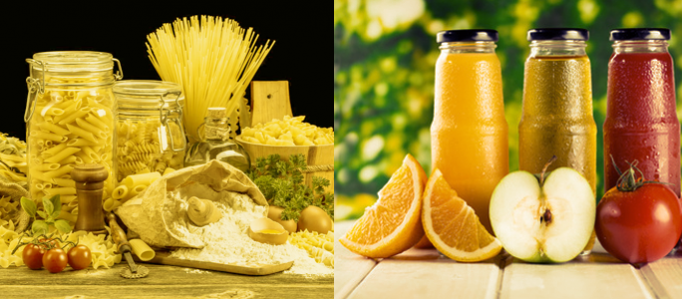
The food & beverages (F&B) industry, which comprises of a number of sub-verticals such as dairy, meat & poultry, beer, edible oil, sweets & confectionery products, packaged food, fresh produce, organic food and other beverages etc., and involves a number of stakeholders, namely the FDA and other regulators, the industry operators like farmers, retailers, distributors and suppliers, and finally the end consumers, is one of the largest industries in the world and largest sectors in the process manufacturing market.
Quite naturally, running a business with so many stakeholders and such wide scope is never easy. Rightly so, the F&B manufacturers face a number of challenges on an everyday basis.
Thin margins, demanding customers, labour complexities, seasonal demands, need for constant innovation & sustainable manufacturing, long & complex supply chains, fierce competition, and stringent regulatory & food safety requirements etc. are some of those challenges which threaten to cripple their day-to-day operations.
In the wake of such challenges, it is important for the F&B manufacturers to develop cost-effective products of highest quality, scale the efficiency to maximize productivity, improve profit margins and meet the consumer expectations while ensuring compliance with the stringent food safety regulations.
In order to achieve all this, the manufacturers look to adopt different approaches.
While some rely heavily on old-school methods such as working on excel and creating multiple spreadsheets, some others opt for multiple disparate systems to manage different functions.
While these methods work, for the time being, they don’t deliver the desired results in the long run. Gradually, your staff is left with the data that is either outdated, inaccurate, or both.
They waste too much time correcting errors with your warehouses, and suppliers, and spend more time dealing with unhappy customers than focusing on doing what they are being paid to do.
This is where the need for the F&B manufacturers to unify their various systems, and have one centralized integrated system arises.
Disadvantages with outdated methods & disparate systems
With a set of old-school methods and disparate systems, getting hold of the right information for the F&B manufacturers can be a time-consuming process.
Most of the times the critical data you need may be locked in complex excel spreadsheets or database, and may frustratingly take more than a day to be decoded.
The presence of disparate systems may even affect the day-to-day functioning of your staff, as they may be forced to spend a substantial time of their day juggling between applications to perform different tasks.
Similarly, everyday operations require a business to pass details between multiple systems, increasing the time taken as well as the risk of error.
For example, records of a sale might be entered into one system, manually sent to the accounts department through the other, and entered into the accounting books through a different system.
Then there’s a new system for managing the information regarding new customers. With disparate systems, there may be a great deal of uncertainty that employees across the enterprise are able to access the most up-to-date information.
But by switching to an integrated solution, you can stay assured of getting all the details you need available at your fingertips all the time.
This way, you can say goodbye to spreadsheets for finding the right financial or pricing details for your products. You can also eliminate the risk of error while manually transferring details between solutions.
How an integrated system does it?
A single, integrated IT system streamlines all the processes. For example your sales team can easily convert quotes into approved sales orders, which automatically flows to Production Manager for planning and manufacturing, forward to the QC manager for quality check, approved materials are then shipped and finally, the finance team receives it for invoicing and revenue recognition, all in the one solution.
Employees can access the relevant files from the single IT solution while simultaneously working on other files – thus saving time and effort that would otherwise have been spent juggling multiple systems.
An integrated system helps eliminate the costs, wait for time and labour normally associated with a set of disparate systems to a great extent, allowing your staff to focus more on their principal tasks.
Such a system can be particularly useful to small and medium-sized enterprises, where any gains in productivity can have a big impact on the firm’s overall performance.
Though it can very well serve businesses of all sizes.
Integrated solutions enable easier sharing and communication among the different parts of the business, and ensure they can always keep in touch with every other part and be confident that everyone is working with the same data.
Why integrated systems for the F&B industry?
Integrated systems are an indispensable part of the F&B industry due to the time-sensitive nature of its products. The empowered consumers these days are aware of every minute detail of what they consume.
They know what it contains, from where it comes, etc. They want fresh food products to be delivered to them. This calls for greater supply chain transparency; something which an integrated system can deliver.
Also, the food products are perishable and come with an expiry date. Handling of perishable products requires careful planning and demand forecasting, as the lack of it can result either in overstocking or understocking.
While the former leads to wastage, the latter results in lost sales. An integrated system connecting all the parts of your F&B business’ supply chain is thus needed to manage your food stock efficiently, allowing you to operate at maximum capacity so that wasted food is minimized, sales opportunities are never missed out on, and profits are maximized.
BatchMaster Manufacturing for SAP Business One for your F&B business needs
BatchMaster Manufacturing (BMM) for SAP Business One for Food & Beverages fully caters to the needs of your F&B business, helping in all aspects of manufacturing, distribution, finance, quality and compliance in the industry.
Its integrated ERP platform includes robust capabilities such as Recipe Management, Production Scheduling, Sales, Procurement, Finance, Inventory and Warehouse Management, Yield and Scrap Management, Quality Control, Material Requirement Planning, Product Costing, Co-Products/By-product Management, Waste Handling, Complaints and Service Management, and more.
Its centralized CRM system helps you serve your clients better, and real-time analytics allows to purchase or produce goods optimally.
With tighter getting laws, it empowers you to follow Good Manufacturing Practices, meet industry standards, manage suppliers plus their certifications, generate labels and comply with FDA, FSMA, FSSAI, and other regulatory bodies.
Its comprehensive Quality Control module restricts movement of material as per quality statuses and supports HACCP, Allergen management, NC/CAPA, stability testing, process testing, and more.
To meet the innovation needs due to changing customer taste and health requirements, BMM for SAP Business One lets you play in your lab without the burden of long calculations to achieve targeted nutritional properties, taste and cost.
Opportunity and Sample Management take care that every request from prospect/customer is recorded, effectively worked upon, plus tracked and cost properly.
Hundreds of recipes and their thousand versions are also efficiently managed, their revisions tracked, every change approved and an audit trail is maintained for each.
Moreover, BMM for SAP Business One for Food & Beverages gives you the speed and insights to reduce operational errors, cut time and costs, and improve response times.
It brings all your business-related data on a single page, allowing you to spend less time getting things together, and empowering you to make better decisions.
Its benefits to your business include accountability of the entire supply chain from vendor to customer, favorable cost calculation, support for GMP guidelines and industry-specific legal standards, easy management of by-products and co-products, reduced errors and ordering time, which leads to on-time delivery, increase in customer satisfaction level, improved overall efficiency, and greater control over the business.
Conclusion:
To achieve a competitive edge in the F&B industry, and to sustain it, many companies are investing in powerful, integrated ERP systems.
Being a world leader in ERP software systems, BMM for SAP Business One is an obvious choice in this regard. BatchMaster has been associated with SAP for last 15 years now.
During this period, being an OEM partner and a value added reseller (VAR) of SAP’s products, BatchMaster has carved a niche and emerged as a force to reckon with in the ERP landscape.
Today, over 3,88,000 customers trust SAP Business One, and SAP Business One trusts BatchMaster for its Process Manufacturing capabilities. For more information on what SAP Business One and BatchMaster together do for the food industry, visit our website or write to us at sales@batchmaster.com.